Take a Tour of our Foundry
Metal casting is a long process involving many steps. Various methods of creating molds into which molten metal can be poured allow an artist’s work to be transferred with great detail to the permanence of bronze, aluminum, or iron.
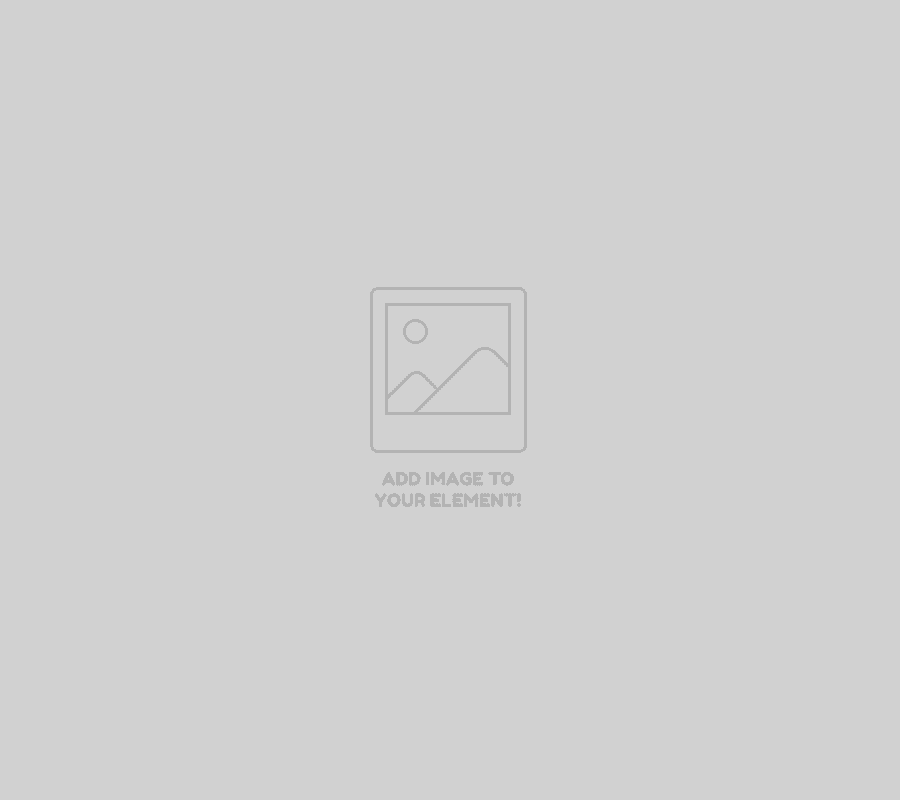
Rubber and Mother Molds
The first step in the process of lost-wax casting is the creation of a rubber mold that can capture detail right down to the artist’s figerprints and allow many faithful editions to be produced over time.
The original item can be almost anything: found object, or sculpture in clay or other modeling material. For a larger sculpture, styrofoam models based on a smaller maquette are often made of the piece or sections thereof.
Metal shims are applied to the original to provide parting lines in the plaster mother mold that will be applied. A layer of rubber is painted over the surface. Smaller items may simply be suspended in a container and have rubber poured around them. Fragile and organic objects can be molded in dental gel. These temporary molds can cast waxes that can be used to make more permanent rubber ones.
Large pieces, however, require a mother mold to support the floppy rubber mold. Plaster is applied in layers and reinforced with burlap for strength. After the mold has hardened, it is pulled away from the shims and removed in sections. When the pattern is removed and the mother mold is re-assembled over the rubber mold, the result is a receptacle into which hot wax can be poured.
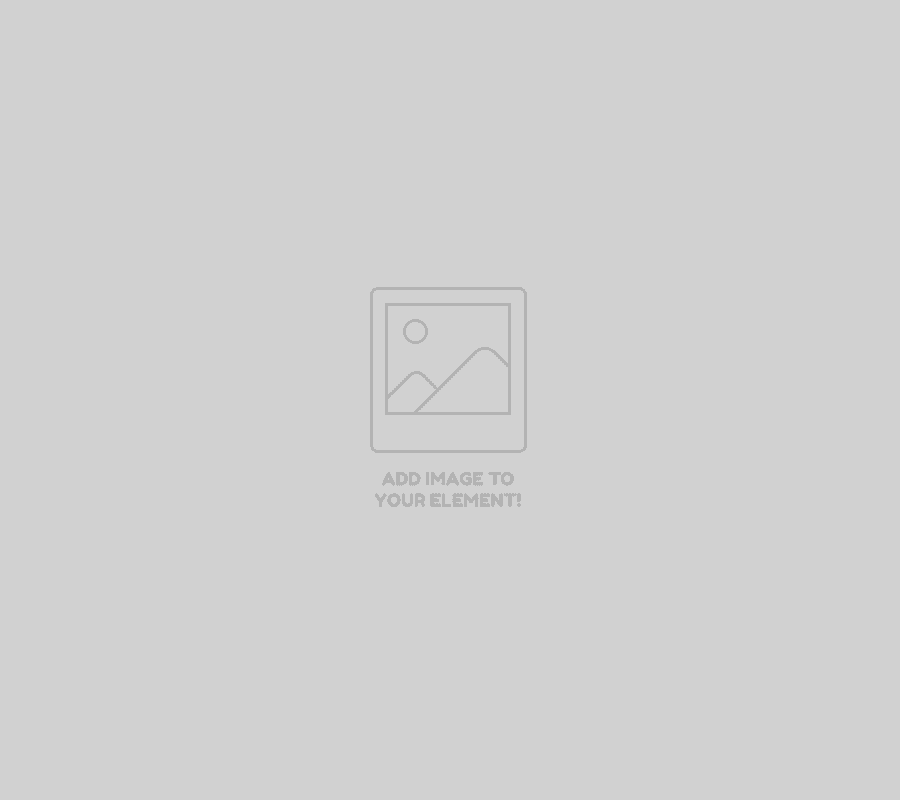
Waxwork
The simplest rubber mold is open-faced like the one below, for a decorative coverplate for a hinge. This is the exception rather than the rule because the surface detail is extremely intricate. Usually a simple piece like this would be sand-molded.
Very large pieces are divided into sections, and in these cases wax is “slush cast.” The mold is rocked and turned to coat the interior with wax. The excess is poured out as it cools and hardens. Several layers of wax are built up in this way, creating a hollow copy of the original.
The wax pattern is allowed to cool and harden enough to remove it by gently pulling away the plaster mother and rubber molds that envelop it.
The wax must now be finished to remove bubbles or any other imperfections, including the parting lines where the sections of the mold came together. This is a meticulous process that greatly reduces the need for surface finishing of the final metal piece. A combination of heat and tools (often clay-working or dental tools) is used to achieve the proper detail in the wax.
When the wax pattern faithfully replicates the original, it is attached to a support structure, a gating system that includes a cup (at the top in the picture at right) where the metal will be poured, as well as runners and sprues from the cup to the gate. In wax, these two elements hold the patterns together but they will be the gateway for the metal in the mold cavity. The small wax rods are vents, which will allow air to escape as metal rushes through the gate into the mold cavity.
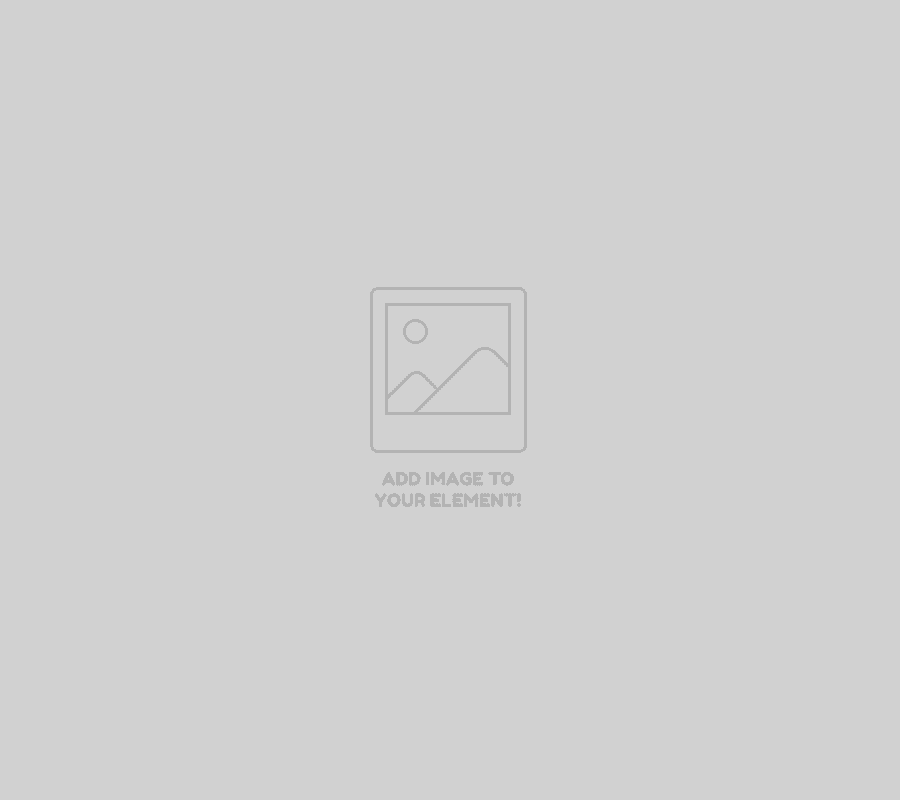
Finishing
After the metal is poured and the castings broken out of their molds, ceramic shell or sand molds are sand blasted or wire brushed to remove any mold residue. Finishing can be a labor-intensive process. The gating and venting systems have to be cut off and ground down as well as parting lines and flashings. Eventually separately cast components are fitted and TIG welded together, their seams chased to blend with their surrounding texture. The surface of the piece is perfected according to our client’s specifications. Some prefer to do their own finishing.
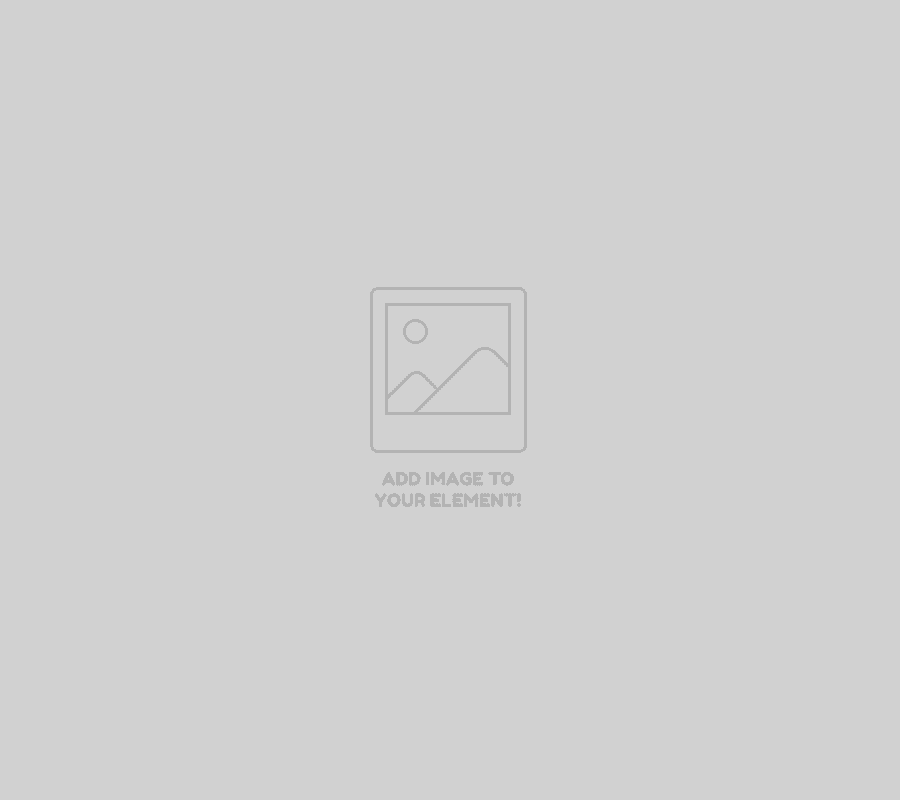
Applying the Patina
Caption under picture of Doris with gas-air torch and pointing statue. “Heating up the bronze with a gas-air torch for a ferric-nitrate patina.”
Applying the patina A patina can be many things. Usually it refers to coloring the metal surface by means of chemical reactions often times with heat to speed the process. It can involve dyes and paint and even plating. There is a nearly endless variety of colors that can be achieved. Generally subdued earth tones survive best outdoors. But no matter where it is, the surface needs to be sealed with wax, lacquer or both to protect the piece. Regular cleaning and waxing will help maintain its original look.
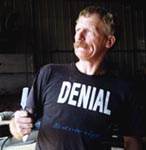