Sculptor’s Guide
Casting in Ferrous and Non-Ferrous Metals
For permanence, distinction and professionalism, cast metal sculpture is unchallenged. Casting allows for accurate replication of texture and complex forms. Metal possesses the strength and structural integrity to open much wider avenues of expression than any other sculptural medium.
Sculpture casting is very demanding; technically intensive and capital extensive. Do-it-yourselfers rarely save money casting their own work unless their expectations are low or they plan to make it a full-time occupation.
False starts and reworks are frustrating and costly. Time and effort can be saved working with a professional art foundry by planning the sculpture from inception through installation. The aim of this essay is to acquaint the artist with some of the processes involved in sculpture casting, point out pitfalls and answer frequently asked questions.
Molding
For casting iron, bronze, and aluminum there are two basic molding techniques: sand and investment casting. These are waste mold systems; in other words, the mold is broken with each casting. Since the high heat of the metal destroys the surface of the mold, they cannot be reused.
There are many different binder systems for sand molds. They bond the sand grains together well enough to allow metal to be poured into the mold and have the mold cavity hold its shape until the metal solidifies. The simplest is a clay-water bond known as greensand. Other “bakeable” binders use molasses or flour. No-bake binders with chemical resins are also utilized. Generally, sand castings require a pattern on which sand mixed with binder is rammed and carefully removed. The pattern must, therefore, be draftable without undercuts (horizontal protrusions or depressions) which will prevent the mold from being pulled from the pattern. Piece molds can be pulled off more complex patterns to avoid undercuts and cores can be used to make bulky pieces hollow for weight saving and to avoid metal shrinkage problems. Patterns which will have many molds taken off them can be made of wood, aluminum or plastic. Some undercuts can be tolerated if flexible rubber patterns are used. Sand casting is usually less expensive than investment casting. Where surface texture does not have to be as highly detailed, it may be the best bet. Many larger pieces are done with the grosser sections done in sand molds while the highly detailed parts such as head, hands, and feet are investment cast.
A variation of sand casting incorporates the investment casting concept of “investing” the pattern in the mold. Polystyrene foam carvings and/or assemblages maybe invested: rammed-up in sand along with a pour cup and lots of vents. The molten metal can be poured through the cup directly into the styrofoam pattern, vaporizing the foam out the vents and replacing it with metal.
Investment casting utilizes the same principle. The pattern is invested in the mold. With lost wax casting, the wax pattern is melted and/or burned out of the mold before the metal is poured in and while the mold is still very hot. It is generally best to make a rubber mold and cast wax patterns from it rather than to invest the one and only original. This practice leaves no reference for the casting/finishing stages. Plus it leaves no “safety net” if the original does not cast correctly. The liability of failure is actually greater since fabricated waxes tend to be weaker than cast ones. Some strength and durability is required of the wax when applying the refractory molding materials. A rubber mold also makes editions possible. An additional benefit of this method is found in the fact that the foundry can store your rubber mold and produce more waxes and metal castings when needed.
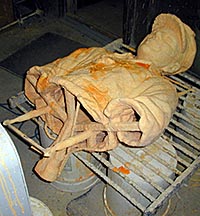
Modeling Materials
Plaster
Plaster is tough and inexpensive. It is not liable to crack, distort, or lose its shape, can be repaired, and is transportable. Be sure the model or platform is properly reinforced with wood, wire, steel, aluminum rods, and/or burlap. If the piece is big enough or complex enough to require disassembly to be molded, be sure it can be easily cut at those points. It is best to have your plaster piece completely finished rather than trying to do final finishing on each wax. It leaves the metal finishers no guide. This ultimately saves time in waxwork, particularly if there is to be a large edition. If a number of sand castings are required, the plaster pattern must be tough enough to stand up to the strain and be draftable. Rubber molds will often pull apart a plaster original although Dental Gel can be used on fragile pieces to obtain a limited number of waxes.
Clay
Unfired clay is very difficult to use for either pattern making, rubber molding, or sand molding. It is liable to break, crack, and distort. Fired clay is much more stable and easy to work with. For sand molding, we prefer to make a rubber pattern of it first. Dental Gel can be used, if necessary, to mold a valuable fragile piece, but it adds expense.
Plasticene
Plasticene is a much better medium for modeling because it does not crack, is easy to repair and can be used over other armature materials such as plaster or styrofoam. Transporting it can be a problem, particularly in warm weather.
Self-Hardening Clay
Self-hardening clay has a lot of the same properties as plaster, but it is more expensive. It can be used thinly over styrofoam for larger pieces.
Resin
Epoxy resin is useful for larger pieces since it can be formed with fiberglass, cloth or mat over Styrofoam, wood, and/or metal armature. Nice surface can be obtained. Detail is difficult. Some plastic patterns may react with rubber molding compound, and leave it sticky or discolored. It is always a good practice to do test samples. Reassembling resin models which have to be cut up to make a rubber or sand molds maybe difficult or impossible. Back to Top
Wood
Wood is an excellent pattern material. Historically, patterns for sandmolding have been wood. Carefully carved and drafted, these were used to make thousands of molds and castings. Wood can also be burned out of ceramic shell molds with an oxygen lance, but some ash which remains may be difficult to remove. Carved wood pieces can be used to make rubber molds quite nicely if wood is waxed, shellacked, or varnished.
Stone
Most stone is okay, but porous stones and marbles should not be used since rubber and sand molds will stick and since binders in those compounds may discolor the originals. Again, Dental Gel can be used for a limited number of waxes from which a more permanent rubber mold can be made.
Wax
Wax is an excellent medium for modeling and is very amenable to rubber molding. Although the original will probably be destroyed in the molding process, plenty more waxes can be produced from the mold. For larger pieces, wax maybe brushed hot over Styrofoam and modeled and carved to achieve the desired surface texture. An armature may be necessary to support a styro pattern and/or spindly waxes. It is good to remember to provide for the possible disassembly of the pattern to facilitate molding.
Styrofoam
Styrofoam can be used as a one-shot pattern invested in a sand mold (it is about the least expensive casting method going). However, the range of possibilities is somewhat limited with this method. As an armature material, styro is extremely useful since it can be covered with a variety of other materials: Epoxy resin, wax, plasticene, plaster and any number of other materials to provide the desired surface toughness and texture. Note that some things react adversely with styrene, notably urethanes and many solvents contained in other materials. It is best to try them on test pieces first.
Bronze and Aluminum
Superficial damage may occur to the patina or paint on these pieces so repatination or painting may be necessary.
Armatures
If an external armature is used, be sure its horizontal stem from the main vertical member gives at least three to four inches separation from the piece. This gives molders room to operate and will help insure a sturdy mold. It is best if the support member falls on the mold’s parting line on the side of the model or pattern.
Wax
Wax Patterns
Waxes cast from rubber molds should be altered as little as possible to avoid losing crisp details. Preferably modifications on these waxes should be carried out at the foundry where tools and skilled assistants are available.
Shrinkage occurs with most materials as liquid turns to solid. Always allow for this shrinkage. The cast wax pattern will be slightly smaller than the original and the metal final casting will shrink still more, as much as a quarter inch per foot. Bismuth is a low melt metal which actually expands as it cools, and is sometimes used to cast patterns slightly oversize to counteract the effects of shrinkage.
We insist that the artist inspect and approve any waxes before we prepare them to be molded for metal casting. Reworking a wax pattern is difficult enough; doing it in metal is very much more time consuming and far more costly.
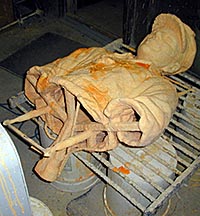
Wax Originals as Patterns
While this is an economical method, it presents some risks. There is no second chance if the casting fails and no guide for repair if part of the casting fails and needs to be redone. Small solid castings may have shrink holes or other surface defects. Most wax patterns from rubber molds are poured one quarter inch or thinner, eliminating this pitfall.
Other materials can be burned out of the ceramic shell molds such as wood and plastic, but may leave residual ash not always readily removable from the mold. Other materials that shrink or expand drastically do not work well: Such as leather and some plastics
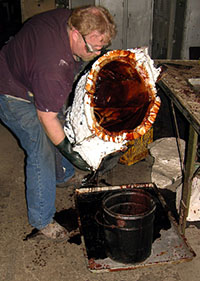
Bases and Mounting
Bases and Mounting
Wood is probably the best bet. We can make arrangements to obtain a base or, in some cases, fabricate simple ones for our clients.
Marble and other stone bases can be special ordered and mounted at the foundry. Artificial marbles made of acrylic resins can be obtained in a great variety of colors. Combinations of wood, stone and plastics are possible too.
A metal sculpture generally needs more than one mounting point to the base or it will tend to pivot on that point. A pin may be mounted close to the main bolt on point to prevent this. The base itself may be formed in such a way as to prevent this pivoting.
Generally, the thickness of the casting at the fixing position must be twice the thickness of the mounting pin and the pin must enter the base by at least a quarter inch.
The minimum size stud for small lightweight sculpture is 1/8 inch, but for larger pieces at least 3/16 to 1/4 inch is necessary. Great hulking outdoor sculptures may need weather resistant stainless steel rods up to 2 inches in diameter to secure them to boulder size bases.
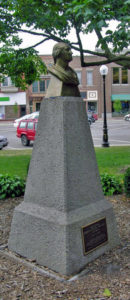
Metals for Casting
Bronze
Bronze is the classic metal of choice for most sculpture. It is easy to cast, malleable, takes a beautiful polish and a great variety of colored patinas. Most foundries use silicon bronzes containing no lead. In general, they are stronger and offer greater corrosion resistance than traditional tin bronze alloys. Silicon brass alloys are available when a yellower color is desired.
The natural color of bronze is hard to define. As the castings are broken from their molds, they are covered with fire scale and other oxides making them look as though they were freshly dredged from the sea floor. Sand blasting leaves them a light straw color. This slightly roughened surface gives sufficient tooth for chemical treatment with various acids and chemicals to bite into the surface. Textured areas generally keep a stronger flavor of the patina and afford greater contrast if they are buffed.
Polished bronze is brilliant and attractive, but expensive due to the extra time needed to perfect the surface. If polished sections are planned be sure to have your pattern’s surface as smooth as possible before the molding process begins. This will head-off snow balling cost overruns. Polished bronze will tarnish unless protected with some sort of clear coat. Unfortunately, no coating will last as long as the polished bronze. You will have to count on removing scuffed, peeled or oxidized coatings and reapplying them from time to time. The artist might consider electroplating portions of the sculpture.
It is very uncommon to pour a large sculpture in one piece. They are usually done in sections. Certain parts of a large figurative piece, for example: head, hands, and feet may be cast using the lost wax method, while the rest of the figure can be done in sand molds, saving considerable time and money.
When additional support is needed for very large works, an internal stainless steel armature may be welded into the sculpture as it is assembled.
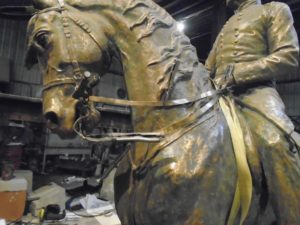
Aluminum and Iron
Where weight and cost are major considerations, aluminum weighs about one third as much as bronze at about half the cost per pound. Large wall-mounted reliefs are often cast in aluminum since they require less structural support.
While it is softer than bronze, cast aluminum tends to be brittle. Thin sections could break under severe stress. It is also rather difficult to weld.
Paint is the usual surface treatment for aluminum castings, but highlights may be sanded and buffed to accent the surface texture. Anodizing can be done on some aluminum although cast aluminum is not the best for it. Outside, aluminum can form white oxides if not clear-coated for protection.
Another phenomenon to be aware of is electrolysis. Joined, dissimilar metals in the presence of an electrolyte such as salty water will act like a battery generating tiny amounts of electricity while slowly dissolving one of the two metals. For this reason stainless steel pins or bolts are often used to secure outside installations since stainless steel is particularly non-reactive.
Cast iron is even more economical than aluminum and may be the most historically correct in some applications. During the nineteenth century, finely detailed, intricate iron castings were as ubiquitous as plastic is today. Of late, iron has enjoyed a rebirth as a sculpture medium. It is superior to bronze in castibililty, since it runs further and picks up greater detail. In corrosion resistance it is a near equal. People often confuse iron and steel. Generally, steel flakes away as it rusts. Iron does not. However, iron does present design limitations. Like aluminum, it tends to be brittle in thin sections and does not weld especially well. Plan for mechanical joints and beefier section thickness especially if the piece may be subjected to any physical abuse.
The sculptor saves by thinking and planning ahead. Realize that the model may need to be cut into sections either for rubber molding or use as a pattern for direct sand molding. Facilitating this saves the foundry time and the artist money. To ensure the various processes continue smoothly, efficiently, and on time, the artist must provide the foundry with all necessary information about the final product at the beginning in the contract stage: wax inspection, metal alloy, base and mounting instructions, surface finish patination (refer to our color patina sheet), edition number, signature and positioning of work (where is the chin in relation to the big toe on the right foot? for example).
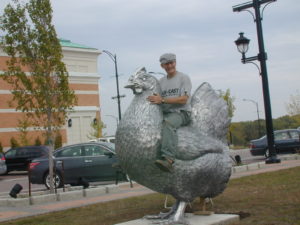
Suggested Reading
Our mission is to bring your vision to reality. We will do our best to help you at each stage of the creative process bringing our expertise and experience to your assistance in every way we can.
The following bibliography may provide more technical know-how:
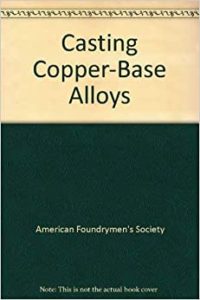
Casting Copper-Base Alloys
Rowley, Mervin T.
Des Plaines, Illinois: American Foundrymen’s Society, Inc., 1984
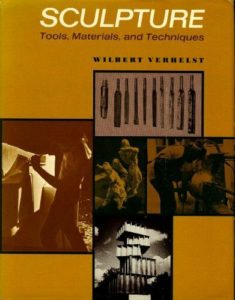
Sculpture Tools, Materials and Techniques
Verhelst, Wilber
Englewood Cliffs, New Jersey: Prentice Hall, Inc., 1987