Your vision. Our commitment.
Let us help you bring your vision to fruition. We have an enormous bag of tricks. We love to trot them out and bring them to bear on what you are interested in getting done. Call us or send an email.
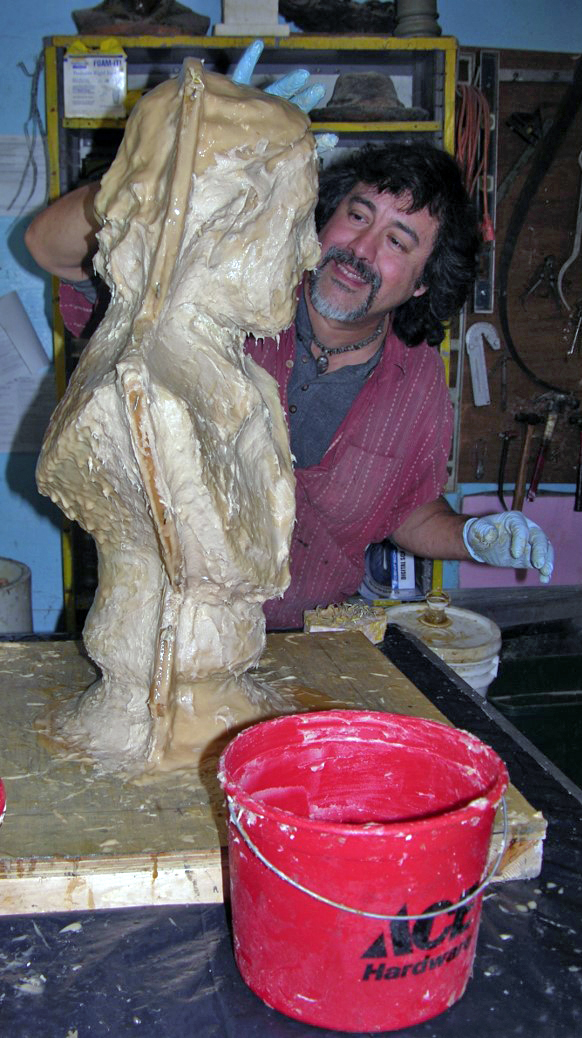
Rubber and Mother Molds
The first step in the process of lost-wax casting is the creation of a rubber mold that can capture detail right down to the artist’s fingerprints and allow many faithful editions to be produced over time.
The original item can be almost anything: found object, or sculpture in clay or other modeling material. For a larger sculpture, styrofoam models based on a smaller maquette are often made of the piece or sections thereof.
Metal shims are applied to the original to provide parting lines in the plaster mother mold that will be applied. A layer of rubber is painted over the surface. Smaller items may simply be suspended in a container and have rubber poured around them. Fragile and organic objects can be molded in dental gel. These temporary molds can cast waxes that can be used to make more permanent rubber ones.
Large pieces, however, require a mother mold to support the floppy rubber mold. Plaster is applied in layers and reinforced with burlap for strength. After the mold has hardened, it is pulled away from the shims and removed in sections. When the pattern is removed and the mother mold is re-assembled over the rubber mold, the result is a receptacle into which hot wax can be poured.
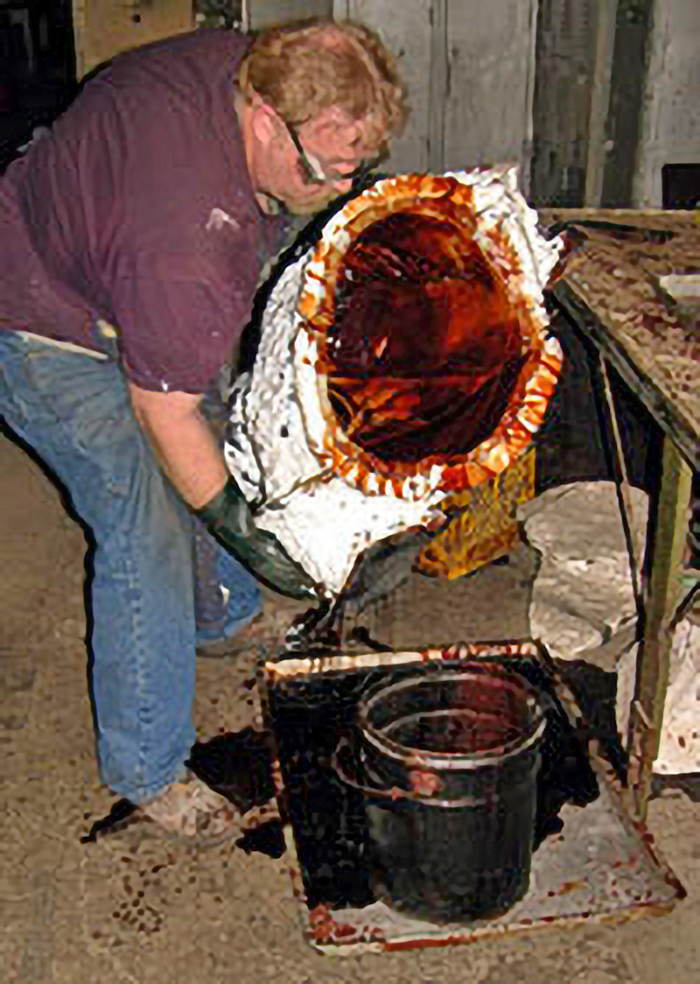
Waxwork
The first step in the process of lost-wax casting is the creation of a rubber mold that can capture detail right down to the artist’s fingerprints and allow many faithful editions to be produced over time.
The original item can be almost anything: found object, or sculpture in clay or other modeling material. For a larger sculpture, styrofoam models based on a smaller maquette are often made of the piece or sections thereof.
Metal shims are applied to the original to provide parting lines in the plaster mother mold that will be applied. A layer of rubber is painted over the surface. Smaller items may simply be suspended in a container and have rubber poured around them. Fragile and organic objects can be molded in dental gel. These temporary molds can cast waxes that can be used to make more permanent rubber ones.
Large pieces, however, require a mother mold to support the floppy rubber mold. Plaster is applied in layers and reinforced with burlap for strength. After the mold has hardened, it is pulled away from the shims and removed in sections. When the pattern is removed and the mother mold is re-assembled over the rubber mold, the result is a receptacle into which hot wax can be poured.
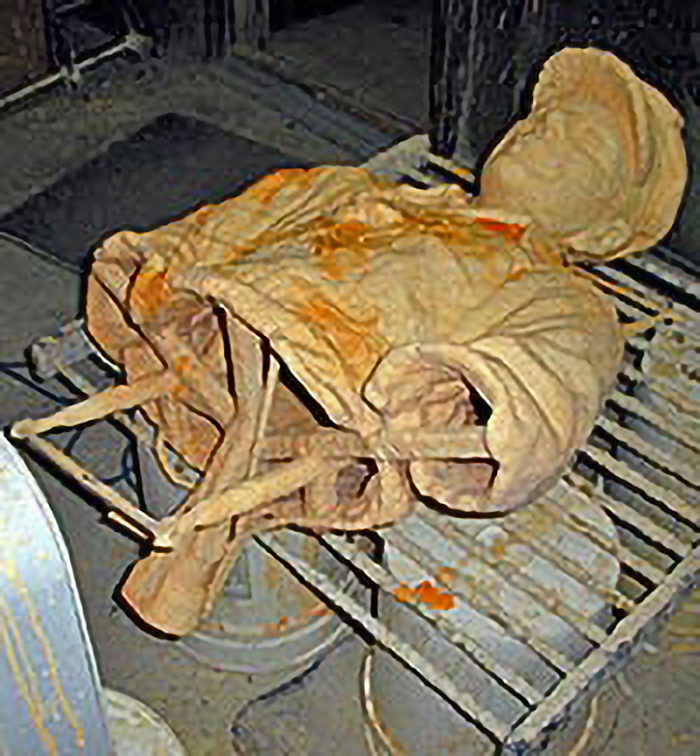
Ceramic Shell
Ceramic shell is a series of refractory coatings on the wax patterns, alternating between slurry and stucco, basically glue and sand.
Completed waxes on sprues are dipped in slurry and stuccoed, and dried between each coat. Usually, 6-12 layers are built up. When the ceramic shell is sufficiently thick (1/4″-1/2″), the wax pattern is burned out, leaving an empty vessel ready to be filled with metal.
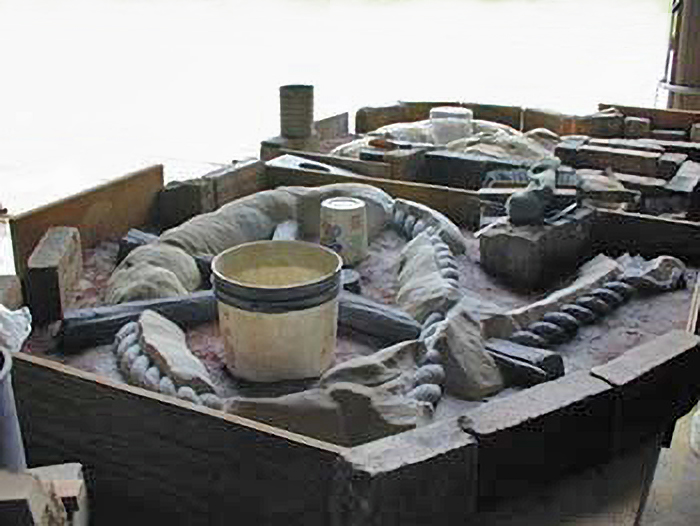
Sand Molding
Sand molding is often overlooked as an alternative to investment casting by most art founderies. It can be very cost effective especially serving as part of a larger piece, say for instance, a large flat base, or plaques, castings problematic for ceramic shell investment. It is more direct than lost wax (no rubber molds or wax work) but requires planning to deal with undercuts and cores for hollow interiors. Occasionally we make rubber patterns that can be pulled out of resin-bonded molds as a way of avoiding piece molding. Since the sand grains are courser than the fine refractories used in ceramic shell, the surface detail is less finely detailed, something that is not always necessary.
Max-Cast mostly uses resin-bonded sand. Molds may also be carved in the negative and assembled for unique sculptures, unseen until cast.
Styrofoam patterns may be invested in sand molds and burned out directly by the metal poured into the mold. Wax can be melted slowly out of sand molds too. We seldom use that technique but often sand mold wax patterns since they can be pulled out of sand molds without excessive piece molding.
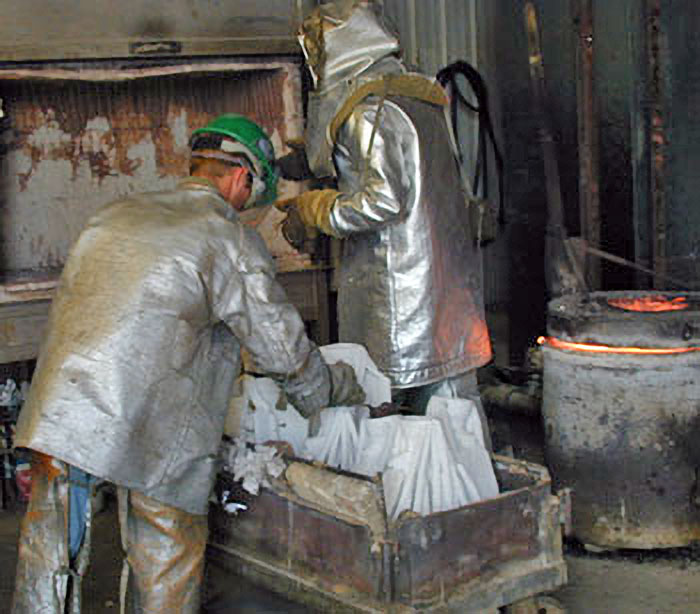
The Pour
Much planning goes into a pour; what temperature should the metal be for each mold, how much to fill it, what order to pour, will the pour cup need to be to be kept hot … The molds represent a tremendous investment of time and effort. There is terrific hydraulic pressure as the molten metal rushes into the mold cavity. It has to hold or the casting could be lost.
Ceramic shell molds are poured hot, anywhere from 800 to 1500 degrees to insure that they fill and catch all the detail in the mold’s surface. Stainless steel wire,” S” hooks and steel “U” clips help them withstand the hydraulic pressure of the inrushing metal and resist runouts. Sand molds are usually rammed up in moist sand in a bottomless casting pit. If there is a runout, the hard-packed damp sand will usually stop it.
Metal temperature is closely monitored with immersion pyrometers to be sure it is right for thin section castings but not too hot for the thick pieces. Aluminum is poured anywhere from 1125 to 1300 degrees, silicon bronze 2100 to 2300 degrees, silicon brass 2000 to 2100, and iron 2400 to 2800 degrees.
Max-Cast mainly uses induction furnaces to melt iron and bronze. They are quieter, cooler and more efficient than our gas-air furnaces, but we still use the combustion furnaces occasionally for aluminum and for one shot bronze castings from 150 to 500 pounds.
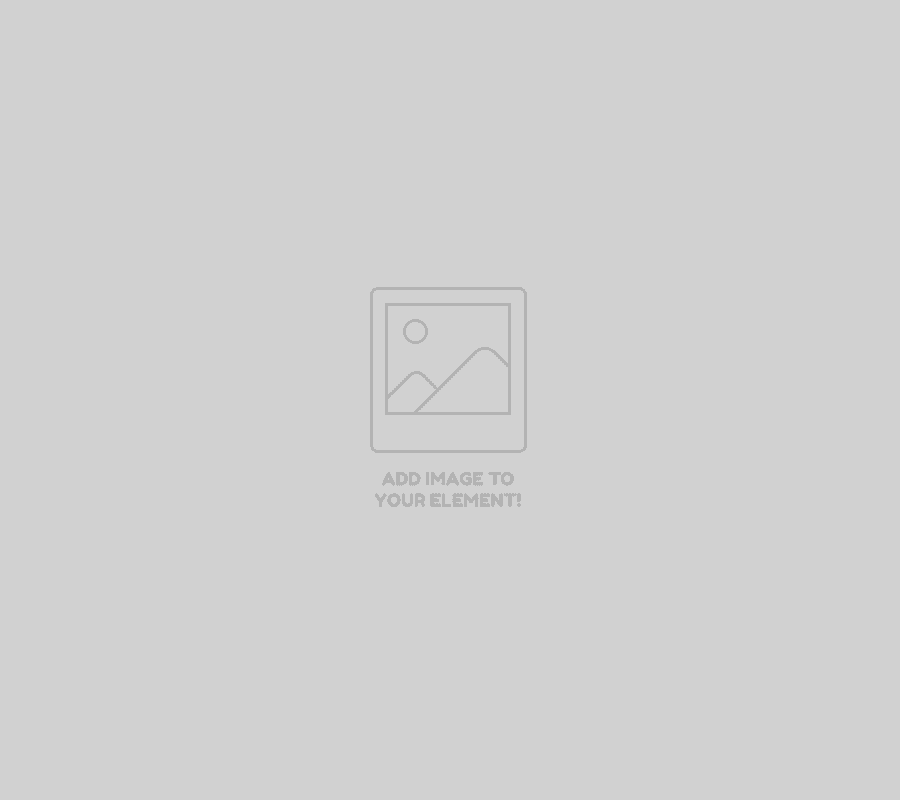
Finishing
Caption under picture: ”TIG welding a pair of bronze eagles”
After the metal is poured and the castings broken out of their molds, ceramic shell or sand molds are sand blasted or wire brushed to remove any mold residue. Finishing can be a laborintensive process. The gating and venting systems have to be cut off and ground down as well as parting lines and flashings. Eventually separately cast components are fitted and TIG welded together, their seams chased to blend with their surrounding texture. The surface of the piece is perfected according to our client’s specifications. Some prefer to do their own finishing.
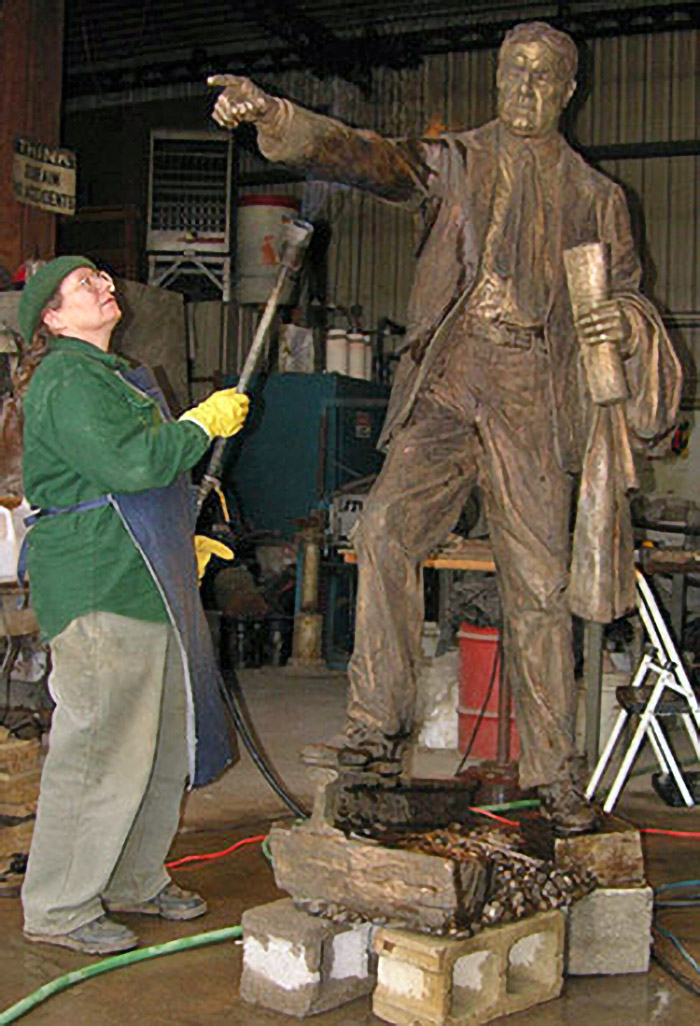
Applying the Patina
A patina can be many things. Usually it refers to coloring the metal surface by means of chemical reactions often times with heat to speed the process. It can involve dyes and paint and even plating.
There is a nearly endless variety of colors that can be achieved. Generally subdued earth tones survive best outdoors. But no matter where it is, the surface needs to be sealed with wax, lacquer or both to protect the piece. Regular cleaning and waxing will help maintain its original look.
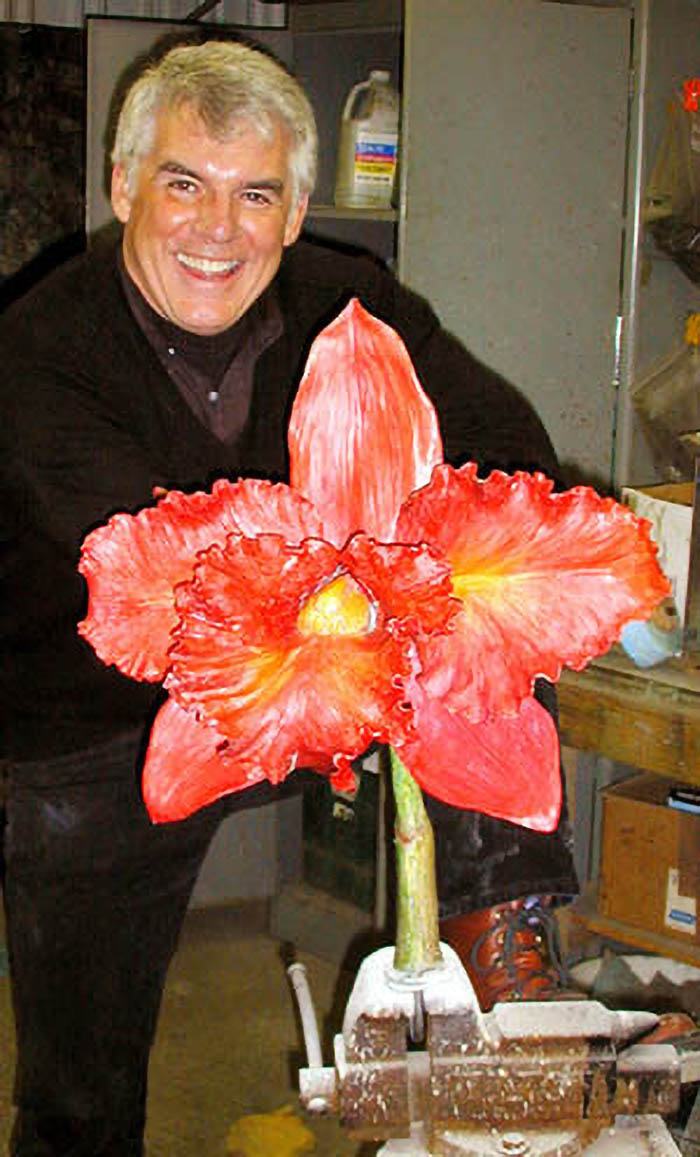
The Pour
Much planning goes into a pour; what temperature should the metal be for each mold, how much to fill it, what order to pour, will the pour cup need to be to be kept hot … The molds represent a tremendous investment of time and effort. There is terrific hydraulic pressure as the molten metal rushes into the mold cavity. It has to hold or the casting could be lost.
Ceramic shell molds are poured hot, anywhere from 800 to 1500 degrees to insure that they fill and catch all the detail in the mold’s surface. Stainless steel wire,” S” hooks and steel “U” clips help them withstand the hydraulic pressure of the inrushing metal and resist runouts. Sand molds are usually rammed up in moist sand in a bottomless casting pit. If there is a runout1 fhe hard-packed damp sand will usually stop it.
Metal temperature is closely monitored with immersion pyrometers to be sure it is right for thin section castings but not too hot for the thick pieces. Aluminum is poured anywhere from 1125 to 1300 degrees, silicon bronze 2100 to 2300 degrees, silicon brass 2000 to 2100, and iron 2400 to 2800 degrees.
Max-Cast mainly uses induction furnaces to melt iron and bronze. They are quieter, cooler and more efficient than our gas-air furnaces, but we still use the combustion furnaces occasionally for aluminum and for one shot bronze castings from 150 to 500 pounds.
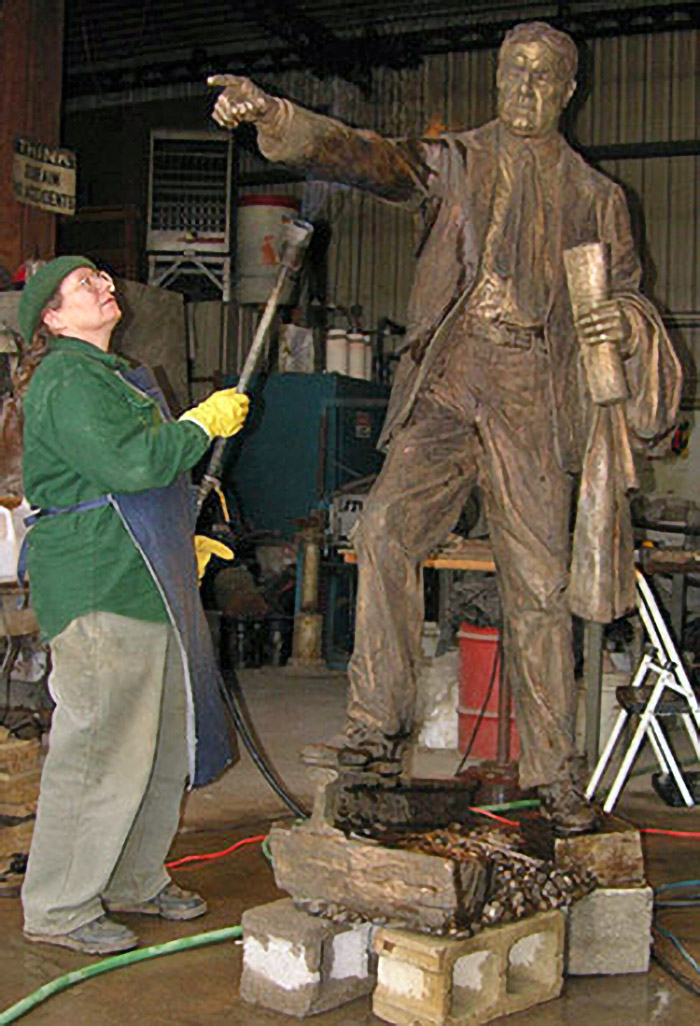
Sand Molding
Sand molding is often overlooked as an alternative to investment casting by most art founderies. It can be very cost effective especially serving as part of a larger piece, say for instance, a large flat base, or plaques, castings problematic for ceramic shell investment. It is more direct than lost wax (no rubber molds or wax work) but requires planning to deal with undercuts and cores for hollow interiors. Occasionally we make rubber patterns that can be pulled out of resin-bonded molds as a way of avoiding piece molding. Since the sand grains are courser than the fine refractories used in ceramic shell, the surface detail is less finely detailed, something that is not always necessary.
Max-Cast mostly uses resin-bonded sand. Molds may also be carved in the negative and assembled for unique sculptures, unseen until cast.
Styrofoam patterns may be invested in sand molds and burned out directly by the metal poured into the mold. Wax can be melted slowly out of sand molds too. We seldom use that technique but often sand mold wax patterns since they can be pulled out of sand molds without excessive piece molding.
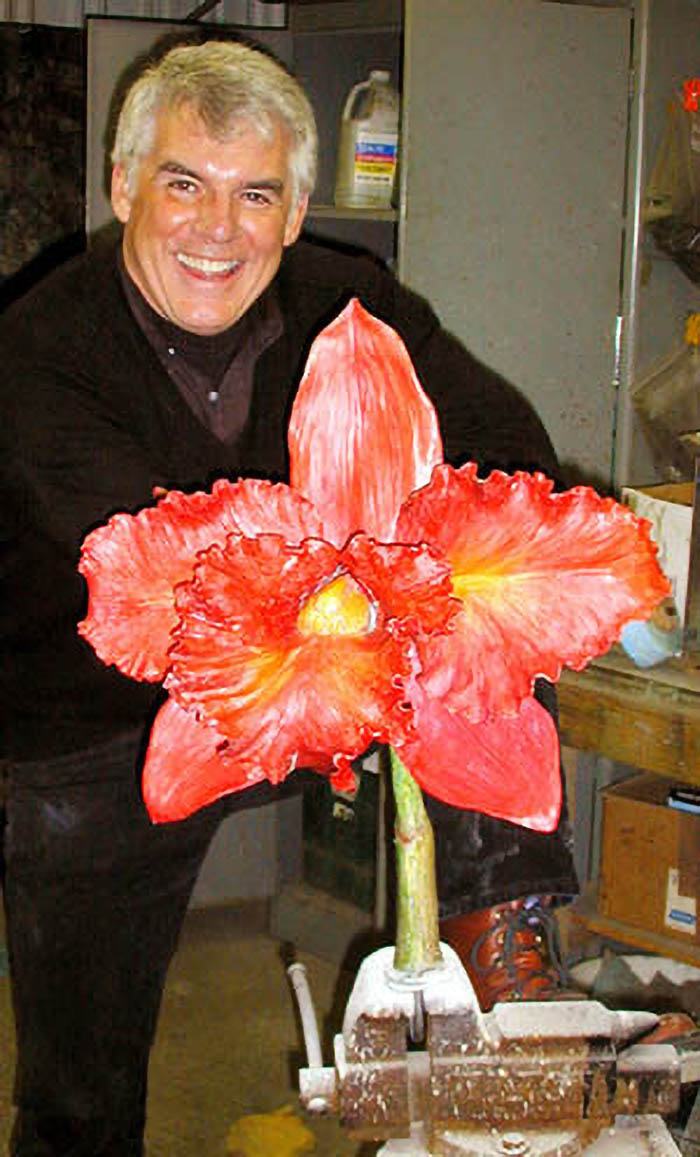
The Finished Product
After weeks or months of work, finishing a large piece gladdens the heart.
Take a look at some of our our current and past custom work, or visit our catalogue to see our in-house sculptures
Thank you for completing the tour!
Foundry Tour
After weeks or months of work, finishing a large piece is a momentous event.
Take a look at some of our our current and past custom work, or visit our catalogue to see our in-house sculptures.
Thank you for completing the tour!
Contact us to take a Foundry Tour at Max-Cast.